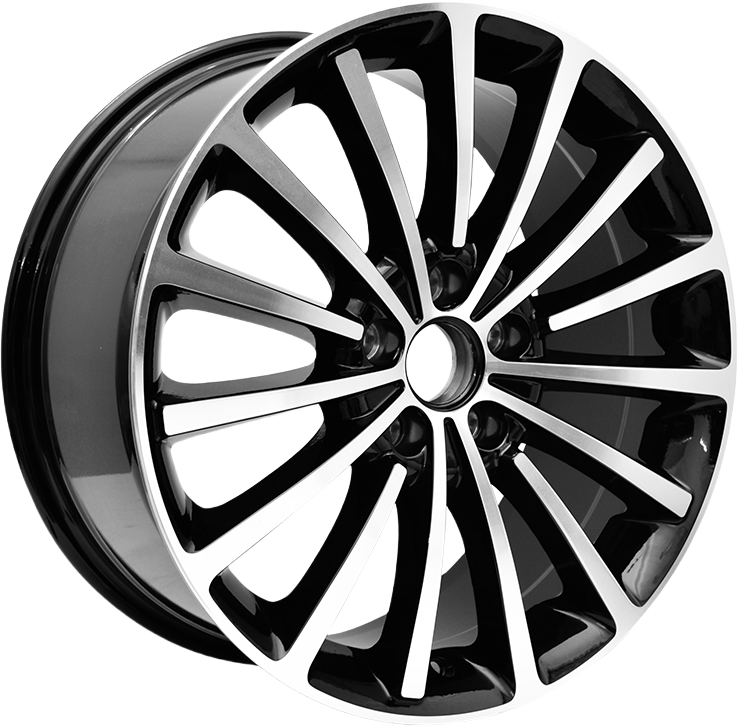
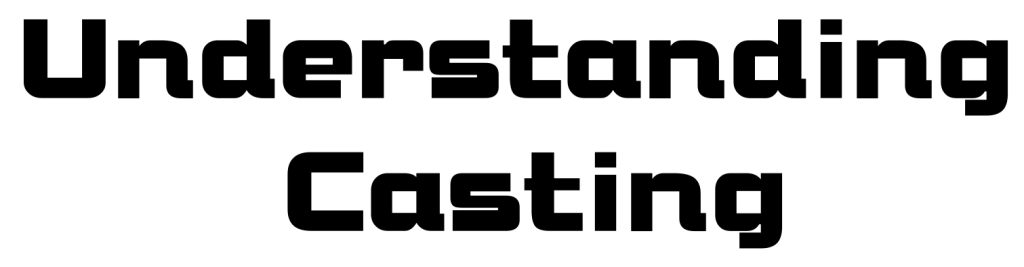
Casting is a process where molten metal is poured into a mold and allowed to cool to form a specific shape. This technique has been used for thousands of years and is a crucial method for manufacturing various metal parts and structures. Depending on the process and equipment used, casting can be divided into several types, with low-pressure casting and gravity casting being among the most common.
Low-Pressure Casting
Low-pressure casting is a method where molten metal is injected into a mold under low pressure. This process is widely used for casting low-melting-point metals such as aluminum and magnesium alloys. The main advantages of low-pressure casting include:
- High-Quality Products: The pressure helps reduce porosity and inclusions, improving the density and mechanical properties of the castings.
- High Precision: This method achieves higher dimensional accuracy and surface finish, reducing the need for subsequent machining.
- High Material Utilization: Better control of metal flow reduces waste and increases material utilization.
- High Production Efficiency: The high level of automation makes it suitable for mass production.
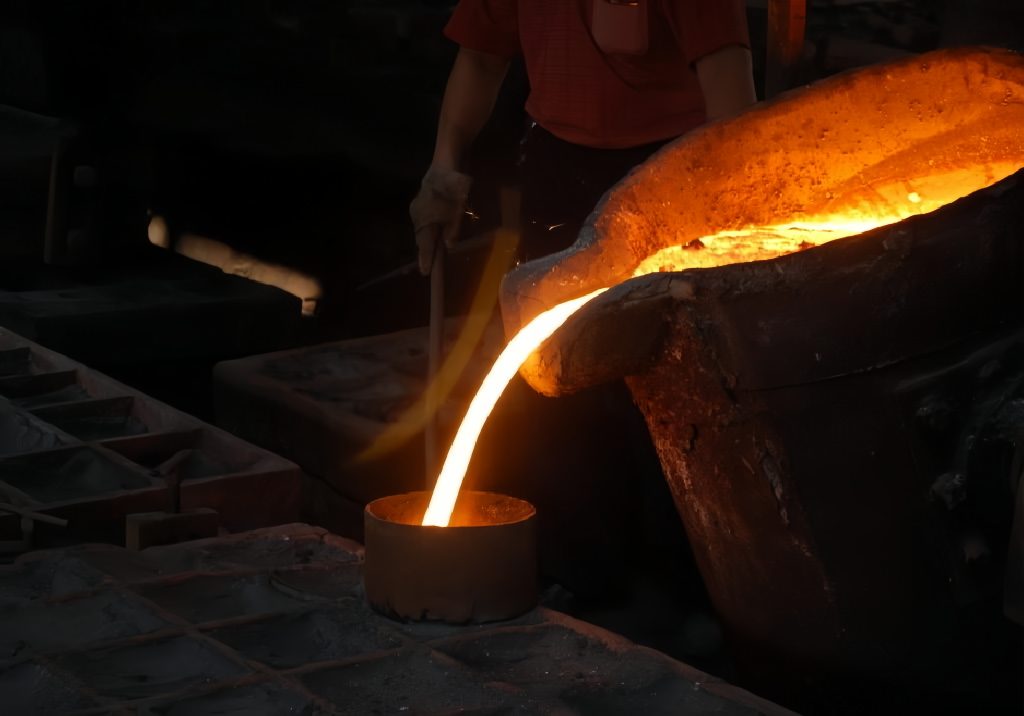
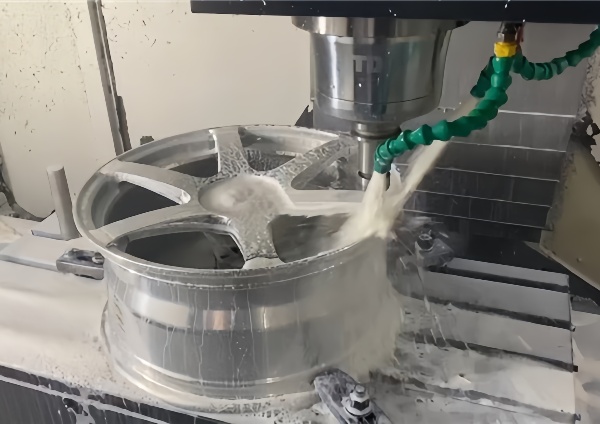
Gravity Casting
Gravity casting is a process where molten metal is poured into a mold using gravity. This method is suitable for various metals, including aluminum alloys, copper alloys, and iron alloys. The main advantages of gravity casting include:
- Simple Process: Lower equipment and mold costs make it suitable for medium and small batch production.
- Wide Application: Can be used for a variety of metal materials with broad applications.
- Long Mold Life: Sand or metal molds used in this process have a long lifespan and are suitable for repeated use.
- High Production Flexibility: Capable of producing castings of various shapes and sizes, offering strong adaptability.